1. Introduction
Optical grating filters in
guided-wave optics have been extensively investigated [1-2], because they
are essential for applications in wavelength division multiplexing
systems. For optical filter applications, high-resolution and high aspect
ratio grating fabrication is important because they impact the filtering
characteristics and compact size of the devices.
Polymeric optical devices are
widely used in guided-wave optics owing to their low cost and simple
fabrication process. Realization of Bragg gratings in polymer waveguides
has attracted much attention in optical communications and optical sensing
systems. Typical techniques for patterning gratings on polymer films
include holographic lithography, electron-beam lithography, laser beam
direct writing, and phase mask lithography. However, few researchers have
focused on fabricating surface-relief grating on channel waveguides.
We have recently demonstrated
a process to rapidly produce submicron range gratings by using both
micro-molding and holographic interference techniques. A large aspect
ratio of 0.7:1 between the depth and the period on the grating pattern
could be obtained, and consistent reproduction of the grating on a UV
polymer could be achieved with this process [3]. In this paper, we
demonstrate a method to inscribe surface-relief gratings on polymer
channel waveguides without any physical etching process.
There are a number of simple
methods to fabricate polymer waveguides that include techniques involving
hot embossing, UV-embossing, and micro-transfer molding method are also
becoming more popular due to their simple fabrication procedure. However,
these methods have problems to overcome; such as residual material
problems and limited substrate and core materials available [4-5]. We have
recently developed a soft lithography method to replicate polymer
waveguides [6]. In this method, the waveguides are produced by a two-step
molding process where a master mold is first formed on a negative tone
photoresist and subsequently transferred to a PDMS mold. The silicone
rubber mold is then used as a stamp to transfer the final waveguide
pattern onto a UV curing epoxy. High aspect ratio (depth/ width) and
vertical waveguide sidewalls could be obtained by this method.
In this paper, we will
describe a technique that combines the holographic interferometry, soft
lithography, and a simple replication processes to create a high
resolution and high aspect ratio grating structure on a polymer waveguide.
In order to reduce the residual stress caused by different thermal
expansion coefficients in the core and cladding material, similar polymer
materials with slightly different index are used for the core and cladding
layers. The material has a refractive index between 1.52~1.56
(OG146=1.5201, and OG154=1.5668) at wavelength 1550nm, which is close to
the refractive index of optical fiber (about 1.46-1.50).
2.
Grating Fabrication
Rapid prototyping of grating
structures on a polymer substrate involving a three-step process was
performed first. A grating pattern is holographically exposed using a
two-beam interference pattern on a positive photoresist film (Ultra 123
made by MicroChem Corp., MA., refractive index = 1.618). This produces a
master that can be subsequently used to produce a polydimethylsiloxane (PDMS)
mold. This silicone rubber mold then is used as a stamp to transfer the
gratings pattern onto a UV cure epoxy polymer. The details of the process
involved for the grating fabrication was described in our previous reports
[3]. Based on our results, we found that the grating period and the
corresponding depth of the grating pattern can be accurately controlled
down to less than 1% error. We also found that a high aspect ratio of
almost 0.7:1 between the depth and the period of the grating structure
could be obtained. Figure 1 shows the AFM and SEM results of OG146 with a
grating period of 503nm and a grating depth of 397nm, which was fabricated
by the above process. The UV polymer with grating was cut down to 1cm x
5cm, and the dimensions of the gratings on polymer were 0.5cm long and 1mm
wide.
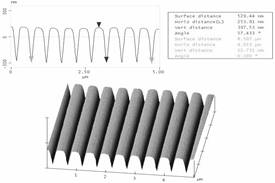
(a)
(b)
Fig.1. AFM and SEM
micrographs of gratings on UV polymer (a) AFM (b) SEM (503 nm grating
period and 397 nm grating depth)
3.
Fabrication of the polymeric
wavelength filter
In order to fabricate polymer
wavelength filters, a 700μm thick glass substrate was first
cut into a 5cm x 1cm rectangle. After substrate cleaning, the UV polymer
was put on the glass, and it was coated with a 6.0 μm thick negative
photoresist (SU-8) spun on at 1000rpm for 17 seconds. Samples were exposed
through the PET (Polyethylene Terephthalate)-based masks using a UV mask
aligner (AB-Manufacturing, CA) for 90 seconds, followed by developing in a
SU-8 developer (MicroChem) for 45 seconds, and negative waveguide pattern
with gratings on the bottom were obtained. The process flow is shown in
Fig. 2(a) and (b). The waveguide dimension is about 8.7μm x 6.0 μm, and
the length is about 5cm. The patterned resist was used as a mother mold to
transfer the pattern onto a polydimethylsiloxane (PDMS) thin film using
typical micro-molding technique(e.g. stamping). The diluted PDMS was
uniformly coated on the patterned photoresist. After baking at 90°C for 1
hr, the PDMS was cured and could be easily peeled off from the photoresist
(Fig. 2(c)-(e)). The waveguide with the gratings pattern was transferred
onto a UV polymer (OG146) from the PDMS mold using a UV replication
process(Fig. 2(f)-(h)). A spacer with a thickness of 400μm was placed
between the mold and a thin Pyrex glass slide. After injection of the
precure UV polymer (OG146), the epoxy was then cured under a broadband UV
light operating in a wavelength range of 300-400nm. After the polymer was
fully cured, the polymer was easily peeled off from the mold. After
separating from the PDMS mold, a hardened epoxy with gratings forms the
cladding layer of the polymer waveguide filter.
To form the waveguide core, a
similar UV epoxy (mixed OG) is injected into the groove. Instead of spin
coating technique, which could create a thick unguided layer outside the
core region that would results in some coupling loss during the input of
the optical fiber to the filter, another method was also proposed (Fig.
2(i)-(j)). A thin layer of a polydimethylsiloxane (PDMS) polymer was spun
onto a glass slide that is then placed over the epoxy groove, forming a
rectangular tunnel. In order to inject the high viscosity epoxy of OG154
into the rectangular channel, we diluted the OG154 with another UV epoxy
OG169 (the mixing ratio is 1:1) to reduce the viscosity of the OG154.
After the curing process, the refractive index of the mixed epoxy is about
1.550 at 1550nm. Then, a drop of the mixed UV epoxy was injected into the
channel from one of the open ends. After exposing with UV light, the epoxy
end of the tunnel was sealed. Next, the sample was inserted into the
liquid epoxy with the open-end face down. This process was performed in a
vacuum chamber (Fig. 2(i)). When the pressure in the chamber reached 10-4
Torr, air was introduced into the chamber to force the liquid epoxy into
the tunnel. The epoxy in the tunnel was cured by exposing the UV light for
1-2 minutes. After the cover glass was removed, the PDMS layer was peeled
off from the sample. To prevent the optical loss due to either surface
scattering losses or the outright absence of a guided mode for the
asymmetric waveguide structure, the upper cladding layer was used. The
same UV epoxy (OG146) was deposited using the fabricating procedure
described in the previous section (Fig. 2(k)-(n)). A spacer with thickness
of 410μm was placed between the sample and a thin Pyrex glass slide. After
injecting the precure UV polymer (OG146) into the opening between the mold
and the glass slide, UV light was used to crosslink the polymer. The
sample were diced and the end-faces were then polished, such that the
final polymeric wavelength filter has dimensions of 4cm in length, 1cm in
width and about 410μm in thickness (Fig. 2(n)).
The waveguide properties
including the mode pattern and the effective index were simulated using
the beam propagation method (BPM_CAD, Opti-Wave Inc., Canada). The
effective index of the waveguide is 1.5447 from the simulation. The Bragg
wavelength is 1553.9 nm as calculated from the Bragg reflection condition.
The transmission of the optical filter was also calculated by using
coupled mode theory[7]. The calculated transmission minimum of the optical
filter is -19.5dB. The spectral characteristics of the optical filter were
measured using an optical spectrum analyzer (Q8384 Optical Spectrum
Analyzer, Advantest Inc., Japan). Again, an amplified spontaneous emission
(ASE) light source with a wavelength range from 1530 to 1560 nm was used
as the wide band light source. An alignment He-Ne laser source, as the
auxiliary source, was combined with the wide band source using a 2×1
optical fiber coupler. The optical filter was set on a micro-positioner,
and two single mode fibers were used as the input and output fibers. The
input light source was polarized in the TE direction as was the mode field
measurement system. The output fiber, then, was connected to the optical
spectrum analyzer to characterize the filter performance. The measured
result is shown in Fig.3. At the Bragg wavelength, a transmission dip of
–18.5 dB was obtained, and the 3-dB-transmission bandwidth was about 8nm.
The result is consistent with the calculation of the coupled mode theory.
The Bragg wavelength λB is given as λB=2NeffΛ,
where Neff, can be calculated using the beam
propagation method, is the effective index of the waveguide grating and Λ
is the period of grating. The measured Bragg wavelength is 1554.02 nm,
which is off by 0.12nm from the theoretical prediction. When the core
refractive index ranges from 1.549 to 1.551 for the ratio of OG154 ranging
from 45% to 55%, the calculated Bragg wavelength by the beam propagation
method varies from 1552.9 to 1554.8 nm.
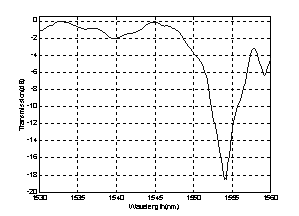
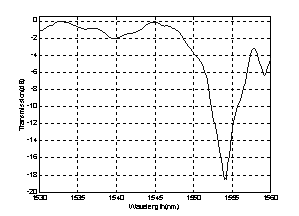
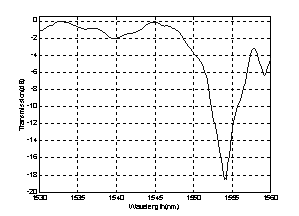
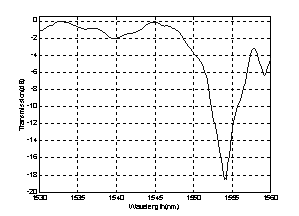
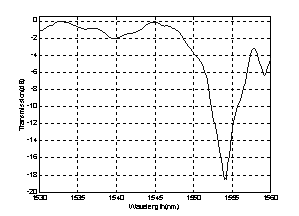
Fig.3.Transmission
spectrum of the polymeric wavelength filter with 0.5cm-long grating length
4. Conclusion
In conclusion, we have
successfully created a process to rapidly produce submicron range gratings
on polymer waveguides by using holographic interference techniques, soft
Lithography, and micro molding. A large aspect ratio grating pattern could
be obtained with consistent reproduction of the grating on a UV polymer
waveguide could be produced. The grating period and depth on the polymer
waveguides exhibited only a small difference from the original designed
grating pattern. This process shows great potential for mass production of
any period of grating structure on waveguide, and could be used to
successfully fabricate coupled polymeric waveguide filters.
References
[1] Y. Shibata, S. Oku, Y.
Kondo, and T. Tamamura, “Effect of sidelobe on demultiplexing
characteristics of a grating-folded directional coupler demultiplexer,”
IEEE Photonics Technol. Lett., vol.8, pp.87-89, 1996.
[2] A.W. Ang, G.T. Reed, A.
Vonsovici, A.G.R. Evans, P.R. Routley, and M.R. Josey, “Effect of grating
heights on highly efficient unibond SOI waveguide grating couplers,”
IEEE Photonics Technol. Lett., vol.12, pp.59-61, 2000.
[3] W.C. Chuang, C.T. Ho, and
W.C. Wang, “Fabrication of a high resolution periodical structure using a
replication process” Opt. Express, vol.13, pp.6685-6692, 2005.
[4] K. E. Paul, T. L. Breen,
J. Aizenberg, and G. M. Whitesides, “Maskless Photolithography: embossed
photoresist as its own optical element,” Appl. Phys. Lett., vol.73,
pp.2893-2895, 1998.
[5] X.-M. Zhao, S. P-Smith,
S. J. Waldman, G. M. Whitesides, and M. Prentiss, “Demonstration
of waveguide couplers fabricated using microtransfer molding,“
Appl. Phys. Lett., vol.71, pp.1017-1019, 1997.
[6] W.C. Chuang, C.T. Ho, and
W. C. Chang, “Fabrication of polymer waveguides by a replication method,”
Applied Optics, vol.45, pp.8304-8307, 2006.
[7] A. Yarin, Introduction
to Optical Electronics, 3rd edition, (H. Rinehart &
Winston, New York, 1984.
.